Producing paper packaging is not a simple process. If you receive a large order that cannot be completed on time. This will probably be the last order you have. Therefore, let’s find out the mistakes to be able to adjust this process quickly.
Not understanding customer needs
This is considered the first mistake that most new paper packaging companies often make. You need to work closely with the client to understand their desires and give advice.
With the number of packaging companies available today, with a single inattention, customers may judge you for not investing enough time in them and turn away from choosing a competitor.
Therefore, quality products are natural. But as a salesperson, you need to advise how good and optimal your paper packaging is, rather than mere words.
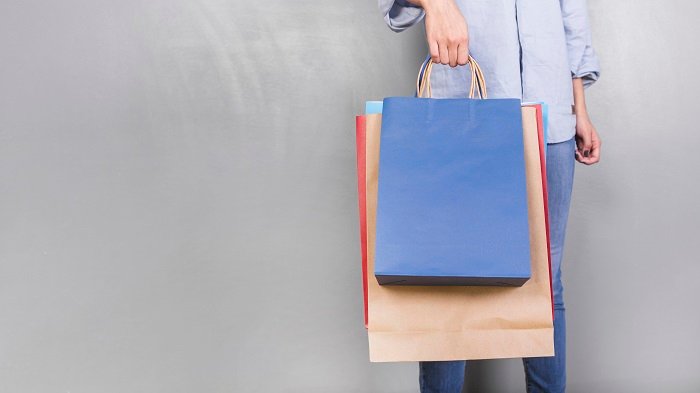
>>> Top 3 factors for evaluating high-quality carton packaging
Make an appointment with the customer so that you can discuss and understand what they expect from the paper packaging projects. Next, send paper packaging samples so that customers can hold them with their hands and see the colors and printing patterns with their own eyes. Then, they can trust and the following stages of work will be much easier.
The paper supply is not clear
The pulp material for papermaking is equally important because it directly affects the user. If the paper supply is unclear, it can make customers doubt the quality of the product.
In particular, with paper packaging directly containing food, clean paper packaging is the first important factor you need to prove to customers in the first transaction. Packaging companies need to meet strict food safety standards such as FSSS 22000, BRC, and so on.
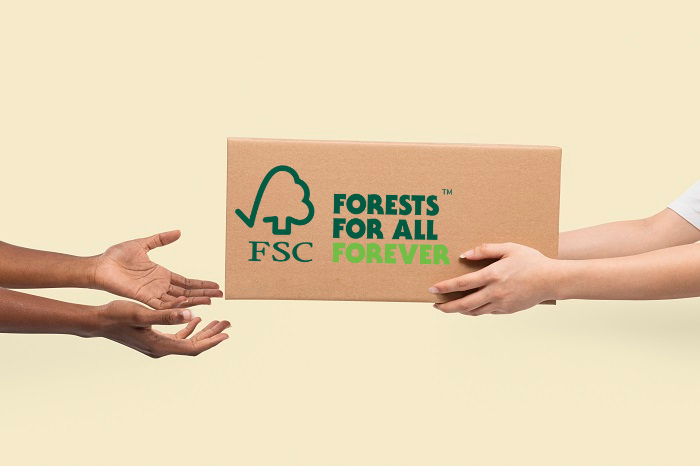
>>> Check 5 benefits of manufacturing paper packaging
No output paper packaging quality check
The next mistake that makes many units lose points with customers is the omission of checking the output quality of paper packaging products. Do not be subjective, because in the production process of anything, there will be defective products.
For large enterprises, the output quality control team is always strong. They will be the ones to monitor and censor the final paper packaging product before it is delivered to the delivery unit. The quality management team at a reputable packaging company will be well-trained and thorough.
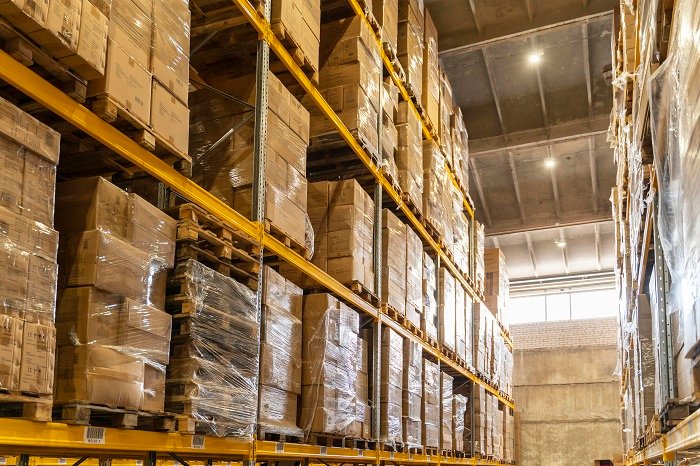
Above all, the packaging manufacturer also needs to develop a strict output quality control process. This helps to reduce the risk of wrong goods, promptly resolve customer complaints and optimize the production apparatus.
Do not receive customer feedback
Finally, don’t forget to accept customer feedback as a “gift”. This will be the most expensive thing to help you see the product’s shortcomings to improve better.
With good feedback, you have more PR tools for corporate services. Whatever it is, accept these things with the warmest and most positive attitude. Because old customers can be future customers and bring you many new customers.
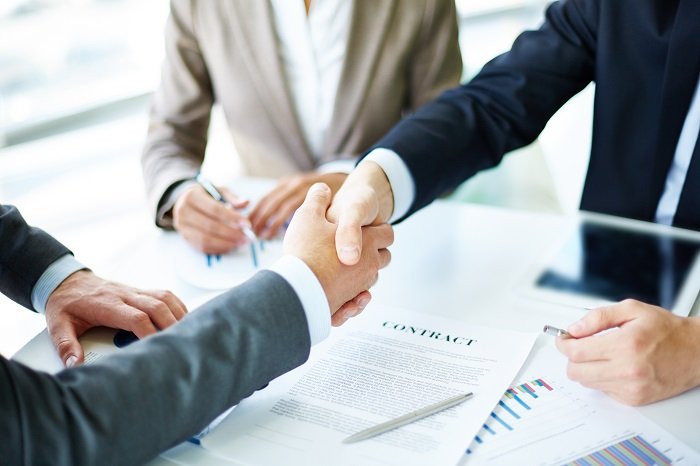
>>> Recycled paper packaging – A trend never out-of-date
The customer service department is really important at this time when it is responsible for collecting customer comments. Then send these to the production and process improvement department. Thereby creating a process that is perfected and upgraded every day.
Hope the above information helps you plan to build your own process. A good product is definitely a guarantee. But customer requirements for quality and standards are something you also need to care about.
KHANG THÀNH – HOUSE OF PACKAGING
Tel: +84 (0) 77 8878 222
Email: info@khangthanh.com